1. Dispersion ability
The ability of a certain solution to achieve a more uniform distribution of coating on an electrode (usually a cathode) under specific conditions compared to the initial current distribution. Also known as plating capacity.
2. Deep plating ability:
The ability of the plating solution to deposit metal coating on grooves or deep holes under specific conditions.
3 Electroplating:
It is a process of using a certain waveform of low-voltage direct current to pass through a workpiece as a cathode in an electrolyte containing a certain metal ion And the process of obtaining electrons from metal ions and continuously depositing them into metal at the cathode.
4 Current density:
The current intensity passing through a unit area electrode is usually expressed in A/dm2.
5 Current efficiency:
The ratio of the actual weight of the product formed by a reaction on an electrode to its electrochemical equivalent when passing through a unit of electricity is usually expressed as a percentage.
6 Cathodes:
The electrode that reacts to obtain electrons, i.e. the electrode that undergoes a reduction reaction.
7 Anodes:
An electrode that can accept electrons from reactants, i.e. an electrode that undergoes oxidation reactions.
10 Cathodic Coating:
A metal coating with a higher algebraic value of electrode potential than the base metal.
11 Anodic coating:
A metal coating with an algebraic value of electrode potential smaller than that of the base metal.
12 Sedimentation rate:
The thickness of metal deposited on the surface of a component within a unit of time. Usually expressed in micrometers per hour.
13 Activation:
The process of making the blunt state of a metal surface disappear.
14 Passivation;
Under certain environmental conditions, the normal dissolution reaction of the metal surface is severely hindered and occurs within a relatively wide range of electrode potentials.
The effect of reducing the reaction rate of metal dissolution to a very low level.
15 Hydrogen embrittlement:
Brittleness caused by the absorption of hydrogen atoms by metals or alloys during processes such as etching, degreasing, or electroplating.
16 PH value:
The commonly used negative logarithm of hydrogen ion activity.
17 Matrix material;
A material that can deposit metal or form a film layer on it.
18 Auxiliary anodes:
In addition to the anode normally required in electroplating, an auxiliary anode is used to improve the current distribution on the surface of the plated part.
19 Auxiliary cathode:
In order to eliminate burrs or burns that may occur in certain parts of the plated part due to excessive concentration of power lines, a certain shape of cathode is added near that part to consume some of the current. This additional cathode is called an auxiliary cathode.
20 Cathodic polarization:
The phenomenon where the cathode potential deviates from the equilibrium potential and moves in the negative direction when direct current passes through an electrode.
21 Initial current distribution:
The distribution of current on the electrode surface in the absence of electrode polarization.
22 Chemical passivation;
The process of treating the workpiece in a solution containing an oxidizing agent to form a very thin passivation layer on the surface, which serves as a protective film.
23 Chemical oxidation:
The process of forming an oxide film on the surface of a metal through chemical treatment.
24 Electrochemical oxidation (anodizing):
The process of forming a protective, decorative, or other functional oxide film on the surface of a metal component by electrolysis in a certain electrolyte, with the metal component as the anode.
25 Impact electroplating:
The instantaneous high current passing through the current process.
26 Conversion film;
The surface facial mask layer of the compound containing the metal formed by chemical or electrochemical treatment of the metal.
27 Steel turns blue:
The process of heating steel components in air or immersing them in an oxidizing solution to form a thin oxide film on the surface, typically blue (black) in color.
28 Phosphating:
The process of forming an insoluble phosphate protective film on the surface of steel components.
29 Electrochemical polarization:
Under the action of current, the electrochemical reaction rate on the electrode is lower than the speed of electrons supplied by the external power source, causing the potential to shift negatively and polarization to occur.
30 Concentration polarization:
Polarization caused by the difference in concentration between the liquid layer near the electrode surface and the solution depth.
31 Chemical degreasing:
The process of removing oil stains from the surface of a workpiece through saponification and emulsification in alkaline solution.
32 Electrolytic degreasing:
The process of removing oil stains from the surface of a workpiece in an alkaline solution, using the workpiece as the anode or cathode, under the action of an electric current.
33 Emits light:
The process of soaking metal in a solution for a short period of time to form a shiny surface.
34 Mechanical polishing:
The mechanical processing process of improving the surface brightness of metal parts by using a high-speed rotating polishing wheel coated with polishing paste.
35 Organic solvent degreasing:
The process of using organic solvents to remove oil stains from the surface of parts.
36 Hydrogen Removal:
Heating metal parts at a certain temperature or using other methods to eliminate the process of hydrogen absorption inside the metal during electroplating production.
37 Stripping:
The process of removing the coating from the surface of the component.
38 Weak etching:
Before plating, the process of removing the extremely thin oxide film on the surface of metal parts in a certain composition solution and activating the surface.
39 Strong erosion:
Immerse metal parts in a high concentration and certain temperature etching solution to remove oxide rust from the metal parts
The process of erosion.
40 Anode bags:
A bag made of cotton or synthetic fabric that is placed on the anode to prevent anode sludge from entering the solution.
41 Brightening agent:
Additives used to obtain bright coatings in electrolytes.
42 Surfactants:
A substance that can significantly reduce interfacial tension even when added in very low amounts.
43 Emulsifier;
A substance that can reduce the interfacial tension between immiscible liquids and form an emulsion.
44 Chelating agent:
A substance that can form a complex with metal ions or compounds containing metal ions.
45 Insulation layer:
A layer of material applied to a certain part of an electrode or fixture to make the surface of that part non-conductive.
46 Wetting agent:
A substance that can reduce the interfacial tension between the workpiece and the solution, making the surface of the workpiece easily wetted.
47 Additives:
A small amount of additive contained in a solution that can improve the electrochemical performance or quality of the solution.
48 Buffer:
A substance that can maintain a relatively constant pH value of a solution within a certain range.
49 Moving cathode:
A cathode that uses a mechanical device to cause periodic reciprocating motion between the plated part and the pole bar.
50 Discontinuous water film:
Usually used for uneven wetting caused by surface contamination, which makes the water film on the surface discontinuous.
51 Porosity:
The number of pinholes per unit area.
52 Pinholes:
The tiny pores from the surface of the coating to the underlying coating or substrate metal are caused by obstacles in the electrodeposition process at certain points on the cathode surface, which prevent the deposition of the coating at that location, while the surrounding coating continues to thicken.
53 Color change:
The change in surface color of metal or coating caused by corrosion (such as darkening, discoloration, etc.).
54 Binding force:
The strength of the bond between the coating and the substrate material. It can be measured by the force required to separate the coating from the substrate.
55 Peeling:
The phenomenon of the coating detaching from the substrate material in a sheet-like form.
56 Sponge like coating:
Loose and porous deposits formed during the electroplating process that are not firmly bonded to the substrate material.
57 Burnt coating:
Dark, rough, loose or of poor quality sediment formed under high current, often containing
Oxide or other impurities.
58 Dots:
Small pits or holes formed on metal surfaces during electroplating and corrosion.
59 Coating Brazing Properties:
The ability of the coating surface to be wetted by molten solder.
60 Hard chrome plating:
It refers to coating thick chromium layers on various substrate materials. In fact, its hardness is not harder than the decorative chromium layer, and if the coating is not shiny, it is softer than the decorative chromium coating. It is called hard chromium plating because its thick coating can exert its high hardness and wear resistance characteristics.
T: Basic Knowledge and Terminology in Electroplating
D: The ability of a certain solution to achieve a more uniform distribution of coating on an electrode (usually a cathode) under specific conditions compared to the initial current distribution. Also known as plating capacity
K: Electroplating
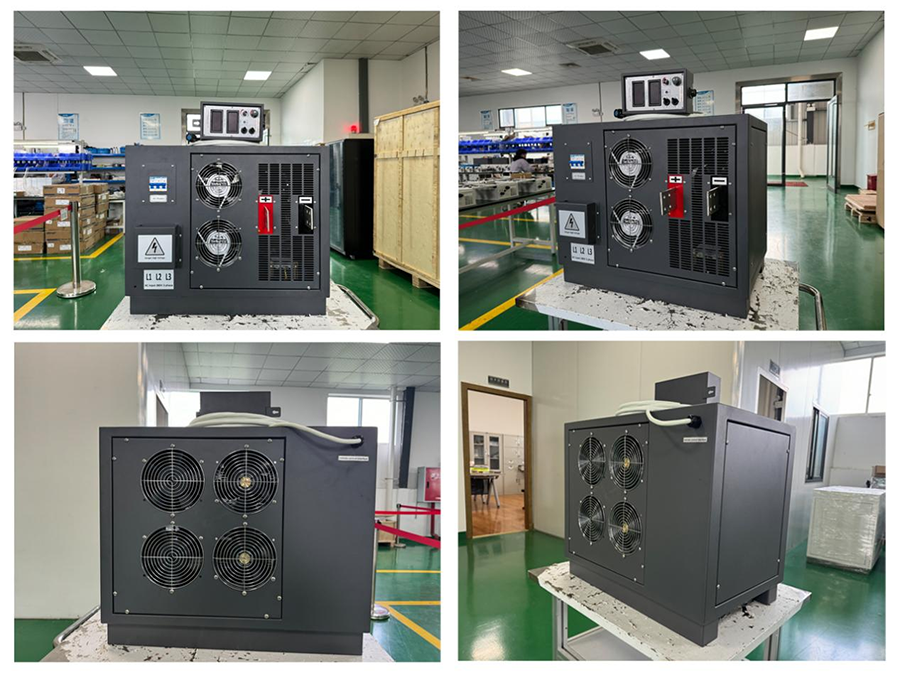
Post time: Dec-20-2024