Anodising is a crucial process in the metal finishing industry, particularly for aluminum products. This electrochemical process enhances the natural oxide layer on the surface of metals, providing improved corrosion resistance, wear resistance, and aesthetic appeal. At the heart of this process lies the anodising power supply, which plays a pivotal role in ensuring the efficiency and effectiveness of anodising operations. Among the various types of power supplies used in this industry, the DC power supply stands out due to its ability to deliver consistent and reliable current, which is essential for achieving high-quality anodised finishes.
A prime example of a DC power supply applied in the anodising industry is the 25V 300A model, designed specifically to meet the demanding requirements of anodising applications. This power supply operates on an AC input of 110V single phase at 60Hz, making it suitable for a wide range of industrial settings. The ability to convert AC to DC power efficiently allows for a stable output that is critical for the anodising process. The 25V output is particularly advantageous for anodising aluminum, as it provides the necessary voltage to facilitate the electrochemical reactions that occur during anodisation.
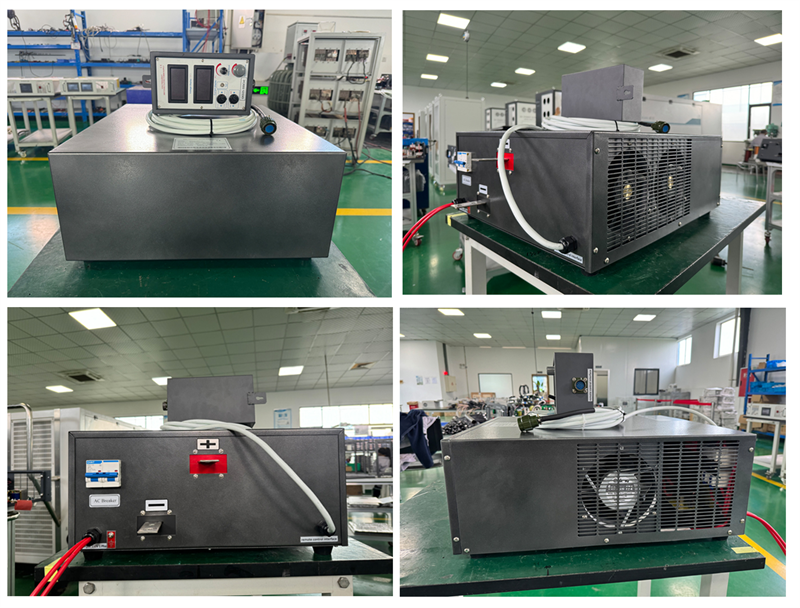
Technical Parameters: |
Product Name: 25V 300A Anodzing Power Supply |
Max input power: 9.5kw |
Max input current: 85a |
Cooling Method: Forced Air Cooling |
Efficiency: ≥85% |
Certification: CE ISO9001 |
Protection Function: Short Circuit Protection/ Overheating Protection/ Phase Lack Protection/ Input Over/ Low Voltage Protection |
Input Voltage: AC Input 110V 1 Phase |
Application: Metal Electroplating, Factory Use, Testing, Lab |
MOQ: 1pcs |
Warranty: 12 months |
One of the standout features of this DC power supply is its forced air cooling system. Anodising processes can generate significant heat, which can adversely affect the quality of the anodised layer if not managed properly. The forced air cooling mechanism ensures that the power supply remains at optimal operating temperatures, thereby enhancing its longevity and reliability. This feature is especially important in high-volume anodising operations where continuous use is required. By maintaining a stable temperature, the power supply can deliver consistent performance, ensuring that the anodising process remains uninterrupted.
Another innovative aspect of this power supply is its remote control functionality, which comes with a 6-meter control wire. This feature allows operators to adjust settings and monitor the anodising process from a safe distance, enhancing both convenience and safety. The ability to control the power supply remotely is particularly beneficial in large anodising facilities where operators may need to oversee multiple processes simultaneously. This flexibility not only improves operational efficiency but also allows for quick adjustments to be made in response to any changes in the anodising parameters, ensuring that the quality of the finished product is maintained.
Additionally, the 25V 300A DC power supply is equipped with a ramp-up function and a CC/CV switchable feature. The ramp-up function gradually increases the current, which helps to prevent sudden spikes that could damage the workpiece or the power supply itself. This controlled approach is essential for achieving uniform anodisation and preventing defects in the anodised layer. The CC (Constant Current) and CV (Constant Voltage) switchable feature provides operators with the flexibility to choose the most suitable mode for their specific anodising requirements. This adaptability is crucial in a dynamic manufacturing environment where different projects may necessitate varying anodising parameters.
In conclusion, the anodising power supply, particularly the 25V 300A DC model, is an indispensable component in the anodising industry. Its robust design, coupled with features such as forced air cooling, remote control capabilities, and adjustable current settings, makes it an ideal choice for both small-scale and large-scale anodising operations. As the demand for high-quality anodised products continues to grow, the importance of reliable and efficient power supplies in the anodising process cannot be overstated. Investing in a high-performance DC power supply not only enhances the quality of anodised finishes but also contributes to the overall efficiency and productivity of anodising operations.
T: The Role of DC Power Supply in the Anodising Industry
D: Anodising is a crucial process in the metal finishing industry, particularly for aluminum products. This electrochemical process enhances the natural oxide layer on the surface of metals, providing improved corrosion resistance, wear resistance, and aesthetic appeal.
K: DC Power Supply anodising power supply power supply
Post time: Nov-06-2024